REcube Postcard from Rome
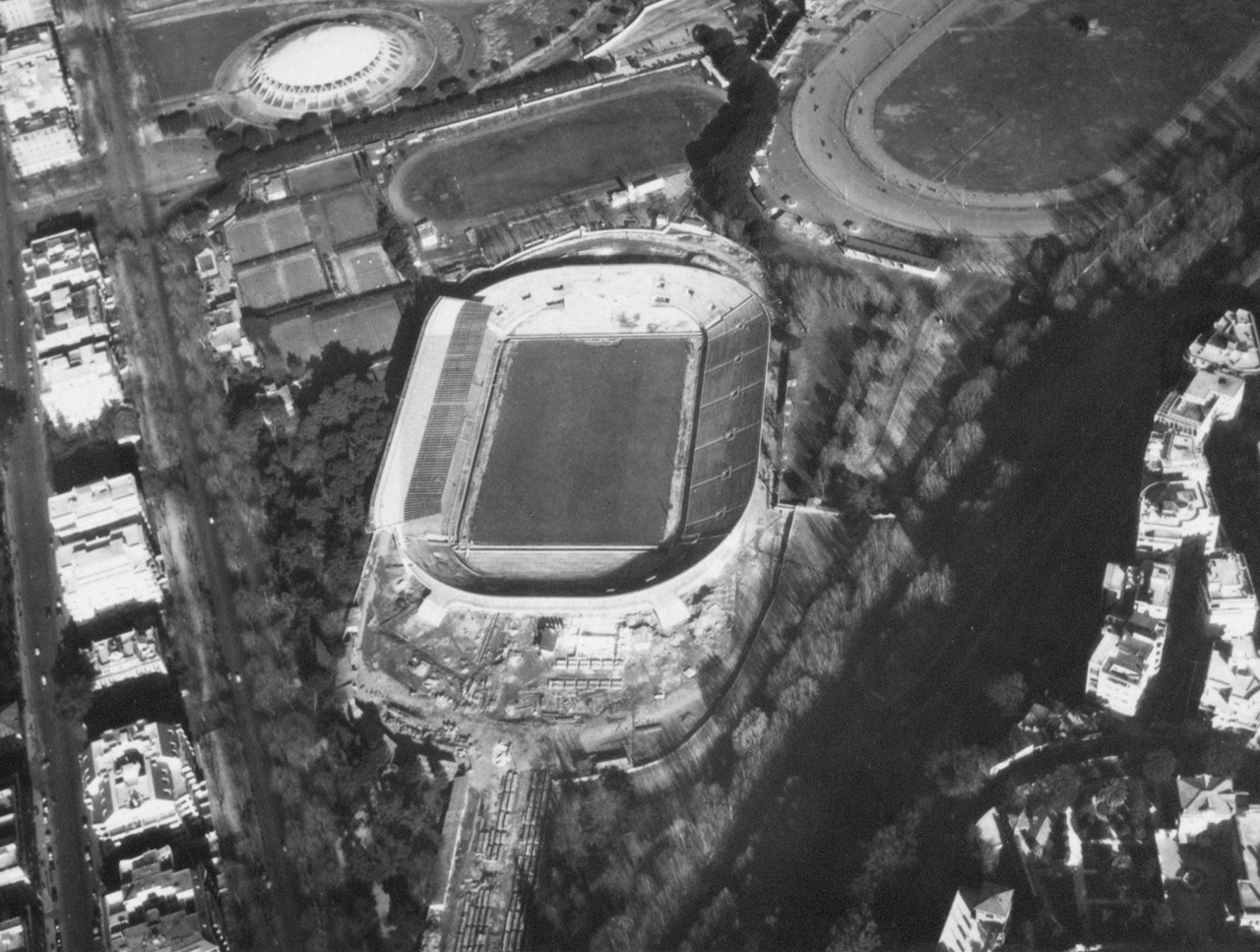
To discover the life and work of Pier Luigi Nervi click here
Pier Luigi Nervi had a very special relationship with Rome, the city where he moved in the early 1920s to start his own business and where he was soon engaged in assignments of all kinds, in Italy and abroad, on his own account or in collaboration with some of the most important architects of the 20th century.
In Rome, therefore, Nervi set up his studio and here he established his construction company. In the Italian capital, Pier Luigi Nervi realised some of his most famous works, ranging across different building typologies and marking forever the urban landscape. At Sapienza University, Nervi taught for a long time, leaving an indelible memory with several generations of architects.
The works realised by Pier Luigi Nervi for the 1960 Rome Olympics, a mature expression of his continuous experimentation, can be considered, from a historical perspective, as true monuments of Made in Italy. At the time of the first TV broadcasted Games, the minutely corrugated or ribbed canopies, the shaped pillars, the isostatically ribbed floors provided an ideal setting for the great Olympic spectacle, helping to spread the image of the Italian miracle throughout the world. A special harmony, the one established between Nervi’s architecture and the Roman Olympics, which today, sixty years later, appears even sharper to us.
Nervi designed and built four masterpieces for the Olympic occasion: the Palazzetto dello Sport set in the Flaminio neighborhood, the Palazzo dello Sport at EUR, the Flaminio Stadium and the viaduct on Corso Francia.
The lightweight structures are emblematic examples of Nervi’s highly personal static concept, which, by exploiting resistance by form in an absolutely original way, reaffirms his adherence to the principle of economy, also as the foundation of aesthetic quality in a built structure.
The Papal Audience Hall was the last of the buildings realised by Pier Luigi Nervi in Rome. At the advanced age of 72, the project for the Audience Hall in the Vatican engaged Pier Luigi Nervi for much of the last phase of his career as a designer. For almost eight years Nervi worked on this structure, which remains unique in his career and represents the last case of a great papal commission, entrusted directly by Pope Paul VI to Nervi, who conceived a building with a strong symbolic and constructive significance for him. Created to welcome pilgrims arriving in Rome to meet the Pope, the Audience Hall is an extraordinarily effective communication machine, capable of involving the worshippers in an experience of meeting the pontiff that is both direct and mediated by the symbolic suggestion of the space.
PIERLUIGI NERVI’S WORKS IN ROME
The Olympic structures: 4 construction sites in 4 years
Chronology of an ‘Italian Miracle‘
On August 25, 1960, the 17th Olympic Games began: the original Italian-made structures framing the event were created by Pier Luigi Nervi not only as designer but also as builder. Within the company Ingg. Nervi e Bartoli, founded in 1932, his sons, who had just graduated, in particular Mario, an engineer, and later Vittorio, an architect, worked in the Olympic building yards during the years of the Olympic Games, as well as his partner, his cousin Giovanni Bartoli; while Antonio, the eldest son, also an architect, joined him in the design studio, which also had a dozen employees and a few external consultants. In the firm, trusted foremen, specialised in the prefabricated pieces of ferroconcrete and the installation of the «Nervi System», are helped by labourers and workforce who mainly take care of the construction on site. The office of the design firm is in the same building where Pier Luigi lives, in Lungotevere Arnaldo da Brescia, while the company has its warehouse in Via della Magliana.
The four construction sites of the Palazzetto, the Stadium, the Palace of Sports and the Viaduct, fit together in time with one another, with the former having to be completed while the plans for the others were being finalised. And these are certainly no ordinary construction sites: the outcomes represent some of the major masterpieces of 20th century Italian engineering and, in particular, of that golden period coinciding with the economic boom.
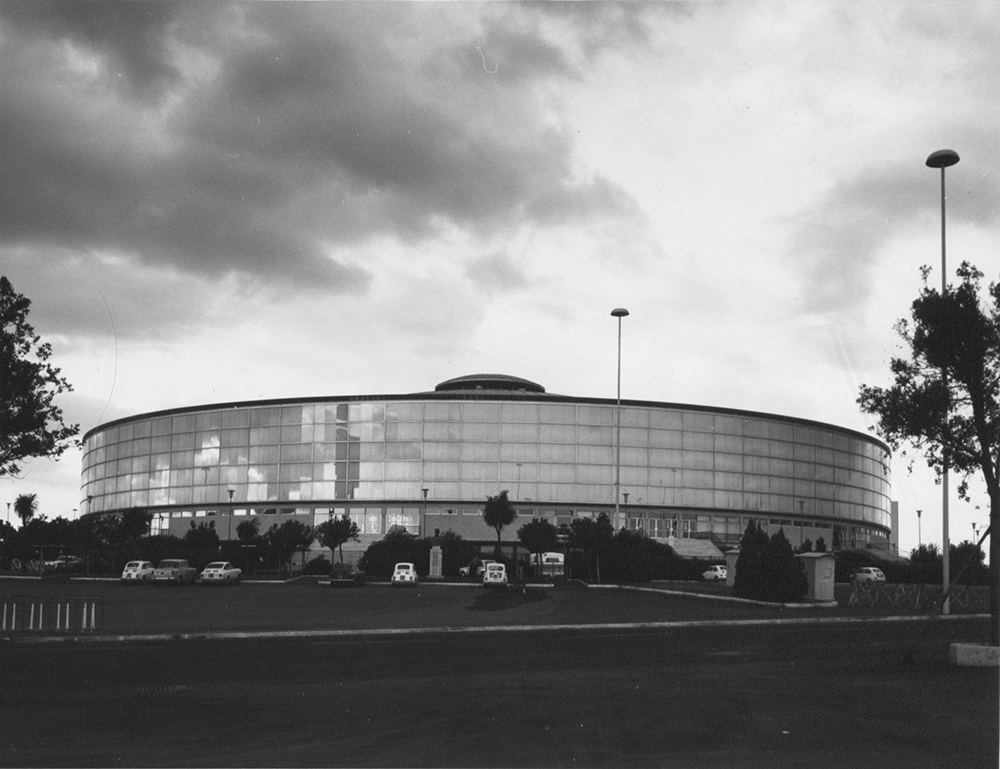
Four masterpieces in four years, then: a feat made possible by the « Nervi System ». All construction sites are completed strictly on time and on budget, with no accidents or injuries to workers. Each work is documented by a dense and orderly photographic sequence: the “photofiches” give us today the dynamics of the construction, almost as if they were the frames of a film.
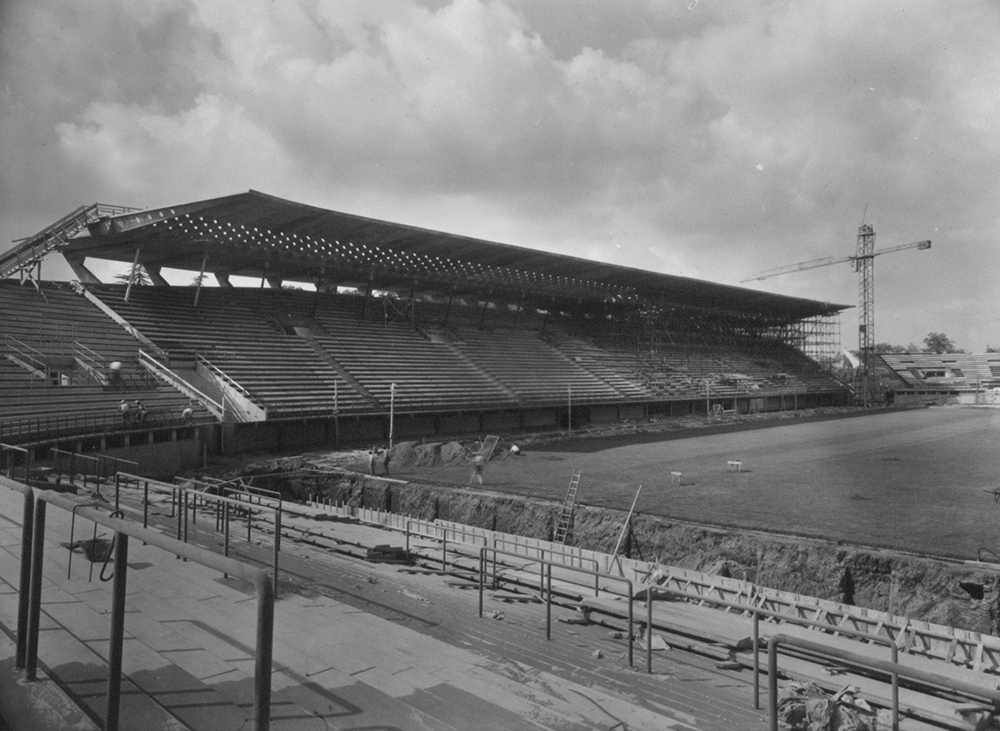
During this demanding sequence of construction sites, Nervi also designed and realised the diving board in the Foro Italico swimming pool and participated unsuccessfully in the Olympic competitions for the velodrome (in particular, the project was drawn up and signed by Antonio) and for the Fiumicino international airport (in addition to designing and realising numerous other structures not related to the Games).
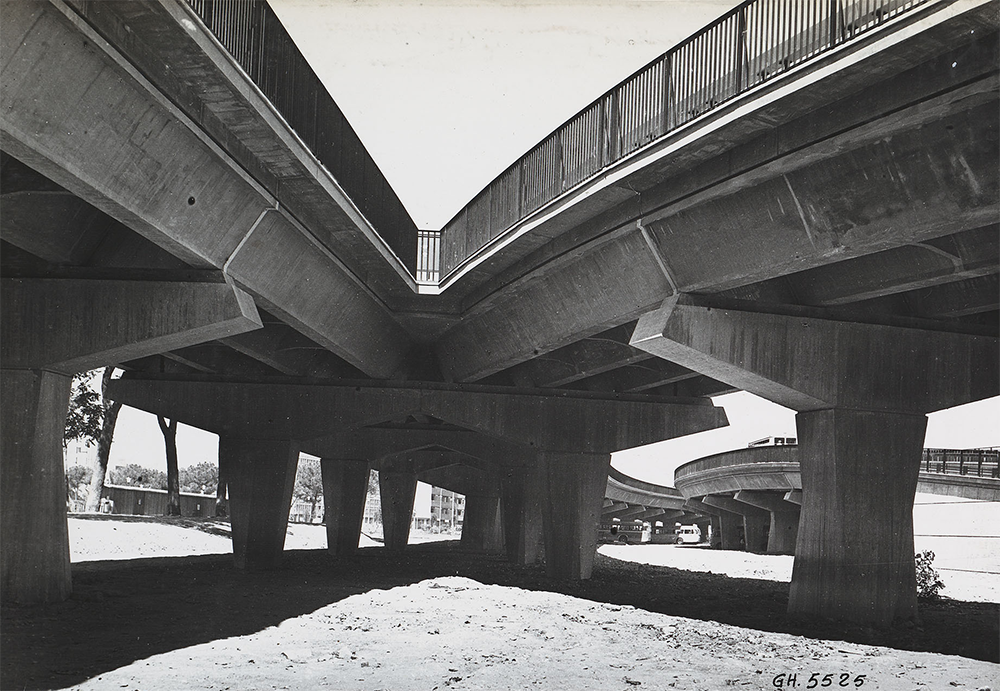
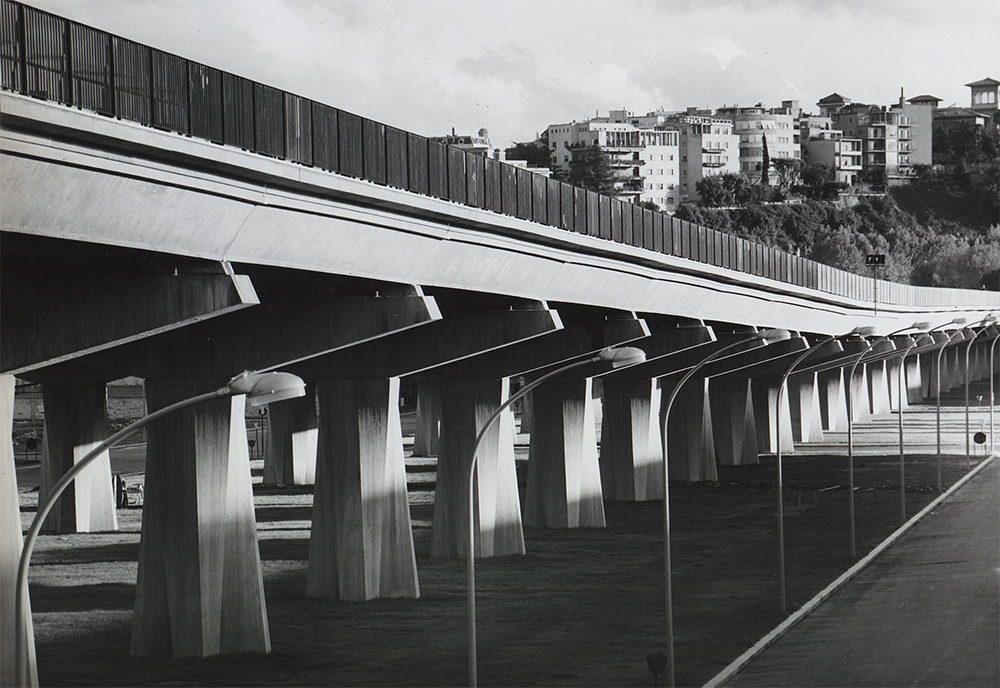
The « Nervi System »
The Nervi System is a set of technical solutions that define a new, economical and rapid way of building. Economical because it eliminates, in the construction process of reinforced concrete, wooden formwork, which is expensive and non-recoverable, and then because it reduces the expense of materials, limiting the thicknesses of the resistant elements (thus decreasing dead weight).
Rapid because it divides the construction site into two autonomous sectors, where workers can work in parallel: on the one hand, the on-site construction site, where excavations are carried out, foundations, pillars and all cast parts are made;
on the other, the prefabrication site, where the pieces that will be used to make up the structures are prepared. The pieces are small and light and are easily moved to the storage site and then to the site in place, which are always contiguous.
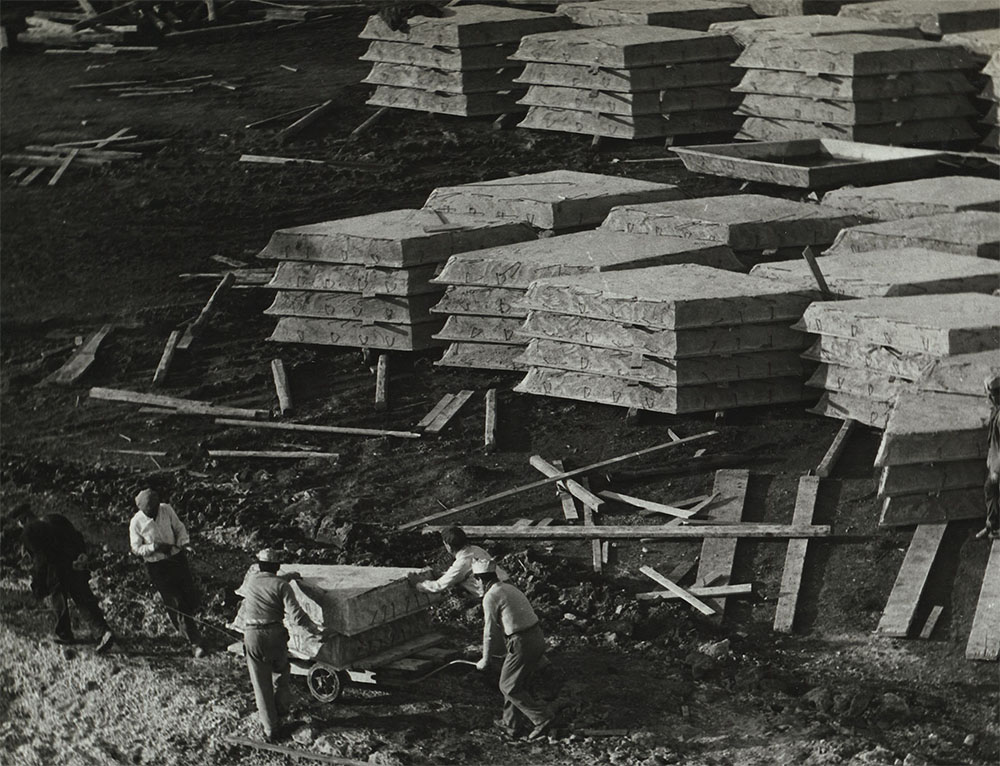
An example of the system’s application is the construction site of the Palazzetto dello Sport.Nervi designs a dome with crossed ribs, drawing many rhombuses with curved sides, which is statically perfect.
With ordinary reinforced concrete it would be too expensive to make, because it would require a very complicated wooden formwork. Nervi, on the other hand, divides the structure into many rhomboidal planks, of a few different types, which when placed side by side, like the pieces of a jigsaw puzzle, compose the overall design.
The rhomboidal pieces are lightweight, and a metal scaffold is all that is needed to hold them in place. The planks function as disposable formwork because they turn up at the edges so that they form, side by side, channels for pouring the cast in place ribs.
The diamond shaped pans are made of ferrocement, a lightweight, formable and inexpensive material. They can be prefabricated on the ground very quickly. For this purpose Nervi uses the stratagem of a sequence of matrices: “grandmother, mother, daughter.” On a wooden template structure, geometrically identical to the inner envelope of a segment of the spherical dome, smoothed with cement, the axes of the rhombuses are drawn and 13 brick templates are made, reproducing the inner cast of the ribbed dome.
A prototype ferrocement pan, called “tavellone”, is made on each of these templates. The prototype, called the “granny,” is not used directly in the construction but is used as a counterform to make 3-4 ferrocement templates, called “moms,” perfectly shaped like the brick ones.
On the “moms,” multiple teams of workers can work simultaneously, under the shelter of a canopy, producing 108 “daughters,” pieces of ferrocement equal to the “grannies” intended to make up the dome. The workers produce, at their busiest times, up to 30 rhomboid pans a day, which are stacked neatly on the construction site.
Meanwhile, on the work-site, the full turn of the trestles is prepared, and in a few months the entire dome can be assembled.
THE PATENTS
In his long career Pier Luigi Nervi filed more than 40 patents: some of these inventions protect his original way of building, the “Nervi System.”
Patent No. 377969 (1939): the “structural prefabrication.”The idea is to break down large reinforced concrete structures into small pieces, to be prepared off-site and then rejoined on site by casting high-strength concrete in the joints. The patent is first conceived and used in the second series of hangars in Orvieto.
Patent No. 429331 (1944): the “ferrocement” (first filed in 1943 with two subsequent supplements).Ferrocement was born during the autarky period, when the use of reinforced concrete was prohibited in Italy because it was not “Italic” (steel for the rods and wood for the formwork were in fact imported from abroad). Nervi, who had always worked only with this material, invents an alternative solution, changing the proportions between the concrete and the reinforcement. He prepares many layers of thin, almost “chicken” wire mesh, and then spreads a conglomerate of high-strength cement and sand over it, resulting in slabs 2-3 centimeters thick. The new material proves to be very strong, elastic, ductile, isotropic, practically homogeneous, lightweight and extraordinarily formable into any shape, and above all, exceptionally cheap.
Patent No. 445781 (1949): the “wave ashlar.”The special wave shaping, easily obtained with ferrocement, allows strength to be exploited by shape instead of mass, resulting in great material economies.
Patent No. 465636 (1950): the rhomboidal pan or “tavellone” and the “grandmother, mother, daughter” system. The ”tavelloni” are made of ferrocement and function as disposable formwork for casting the ribs. The patent partly includes the generative process, i.e., the “grandmother, mother, daughter” sequence, which provides great time savings on the construction site.